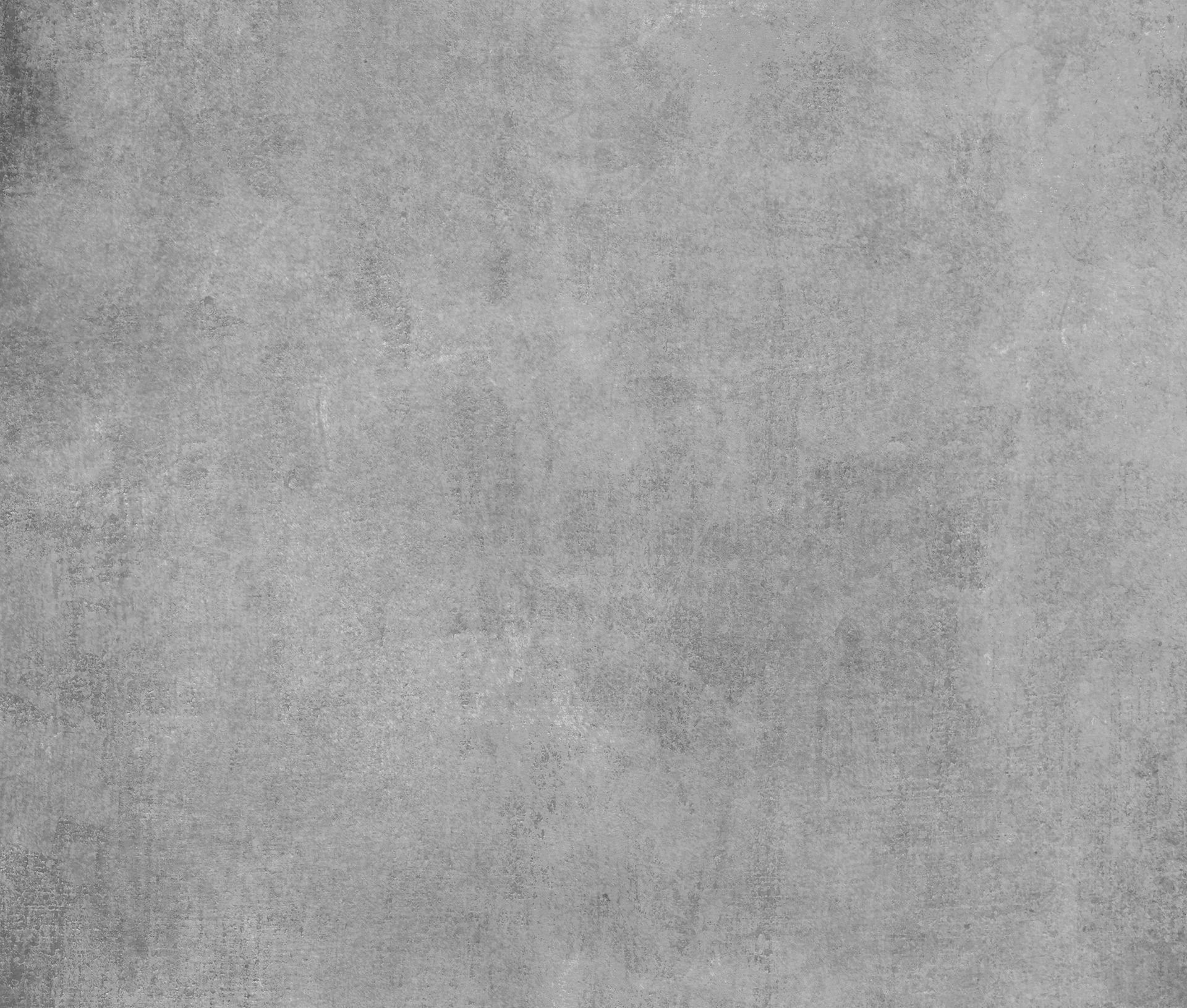

PORTRAIT ARTIST

Casting bronze
Most professional sculptures are cast into bronze by the traditional lost wax method, originally developed by the Chinese about 6 thousand years ago. This results in a bronze duplicate of the original piece. This process is normally done by a separate foundry, not the artist. Philip uses Talos Art Foundry where he is involved in the process. Bronze will stand in the elements for many years without requiring much maintenance.
On receiving the artwork from the artist, a plan is agreed on how the sculpture will be cast. Simple small pieces can be straightforward and cast in one mould, but complicated items may be made in many parts and welded back together later in the process.
On receiving the artwork from the artist, a plan is agreed on how the sculpture will be cast. Simple small pieces can be straightforward and cast as one mould, but complicated items may be made in many parts and welded back together later in the process.
Below is a simplified explanation of the process. As shown, this is highly labour instesive and requires many separate skills. This results in a quality items which will last for many decades.
Pouring molten bronze at 1200C
Process
1. The sculpture has first hard shell created round it with a gap between the subject and the shell so that a latex mould can be created. This takes up the detailed surface and structure.
​
2. Once the latex has hardened, the shell is opened then removed from the latex which often damages or destroys the original work.
3. The mould is then reassembled and inverted and green wax is then poured in latex.
​
4. When cooled the wax copy of the item is removed from the mould.
​
5. The green wax will have imperfections and lack clarity, so the artist prepares it for the next stage adding lost detail and filling any voids.
6. Sculptures are not necessarily in the ideal shape to cast unless there are clear routes where the molten metal can flow and trapped air can escape. To facilitate this process, thin wax “sprue” rods are added to the wax sculpture called runners and risers.
7. A pouring cup is fitted to the base into which then inverted thus permitting a spout where the molten metal is poured.
8. The wax structure is then covered in ceramic or silica material to form the casting mould for the metal.
9. When the ceramic has hardened the wax melted out of ceramic using a hot oven leaving a void in to which the metal can be poured.
10. The ceramic mould is then heated gently heated to a similar temperature to molten bronze to prevent it shattering due to the temperature difference.
11. The solid cold ingots of bronze are then heated in a furnace.
12. It is then transferred into a crucible, to be transported and poured into our mould.
13. The inverted ceramic mould is then filled with molten bronze at roughly 1200 °C.
14. The ceramic moulds and the bronze are then allowed to cool and when it’s safe to work on it is then chipped from ceramic cast.
15. The runners and risers are cut off with grinders and everything is cleaned. Where necessary, pieces may be welded back together. If the work is large, say a life-size horse and rider, this is a significant process.
16. The bronze is chased and cleaned and imperfections and welds are made invisible.
17. Support or stand fitments can then be welded to the sculpture.
18. At this stage, the sculpture is a bright yellow metal and, normally not the finish that the client or artist desire so it is now ready to be patinated.

Green wax sprue ready for use
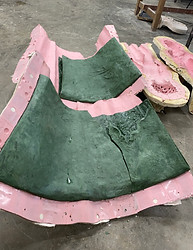
Parts of a 7 foot sculpture in green wax laying in the latex mould. They are supported in their white hard shells.
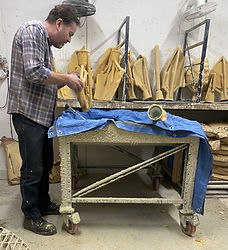
Preparing the green wax inside the ceramic moulds
_HEIC.jpeg)
Green wax copy from the original sculpture
Patination
This is either a natural process that forms over the metal during the passage of time, or a chemical treatment for decorative or artistic purposes. It is therefore just on the outside of the metal, and should the sculpture be damaged, the bright metal will show through. Patination can also be protective against the elements and a wide range of colours can be achieved.
The final process is applying coats of hot wax over the previously heated metal. This brings out the lustre and deep colours of the patination.

Test patina examples